See This Report about Alcast Company
See This Report about Alcast Company
Blog Article
The Facts About Alcast Company Uncovered
Table of ContentsAll about Alcast CompanyAn Unbiased View of Alcast CompanyAlcast Company - TruthsExcitement About Alcast CompanySome Known Incorrect Statements About Alcast Company All About Alcast Company
The refined distinction depends on the chemical content. Chemical Comparison of Cast Aluminum Alloys Silicon promotes castability by lowering the alloy's melting temperature and enhancing fluidity during casting. It plays a vital duty in enabling elaborate mold and mildews to be filled properly. Additionally, silicon adds to the alloy's strength and put on resistance, making it important in applications where toughness is critical, such as vehicle parts and engine components.It also boosts the machinability of the alloy, making it less complicated to refine into ended up items. In this way, iron adds to the total workability of light weight aluminum alloys.
Manganese adds to the toughness of light weight aluminum alloys and enhances workability (aluminum foundry). It is frequently utilized in functioned light weight aluminum items like sheets, extrusions, and profiles. The visibility of manganese help in the alloy's formability and resistance to breaking throughout fabrication processes. Magnesium is a lightweight element that provides stamina and effect resistance to light weight aluminum alloys.
The 30-Second Trick For Alcast Company
It permits the manufacturing of light-weight elements with outstanding mechanical residential properties. Zinc boosts the castability of light weight aluminum alloys and aids regulate the solidification process throughout spreading. It improves the alloy's toughness and solidity. It is typically found in applications where elaborate forms and fine details are needed, such as attractive castings and certain auto components.
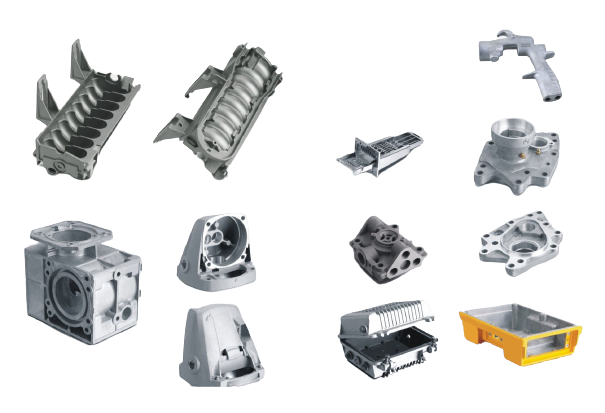
The key thermal conductivity, tensile toughness, return toughness, and elongation differ. Among the above alloys, A356 has the greatest thermal conductivity, and A380 and ADC12 have the lowest.
Alcast Company Fundamentals Explained

In accuracy spreading, 6063 is well-suited for applications where elaborate geometries and top quality surface finishes are vital. Instances include telecommunication units, where the alloy's remarkable formability enables sleek and visually pleasing styles while preserving architectural integrity. Similarly, in the Lighting Solutions sector, precision-cast 6063 elements produce classy and efficient illumination fixtures that require intricate shapes and great thermal efficiency.
The A360 exhibits remarkable elongation, making it suitable for complicated and thin-walled components. In accuracy spreading applications, A360 is fit for sectors such as Customer Electronic Devices, Telecommunication, and Power Tools.
The Best Strategy To Use For Alcast Company
Its distinct residential or commercial properties make A360 a valuable option for precision casting in these markets, boosting product sturdiness and high quality. Aluminum alloy 380, or A380, is a widely utilized spreading alloy with numerous distinctive qualities. It supplies excellent castability, making it a suitable selection for accuracy casting. A380 displays great fluidness when molten, ensuring intricate and thorough molds are precisely replicated.
In accuracy spreading, light weight aluminum 413 shines in the Consumer Electronic Devices and Power Devices sectors. It's frequently utilized to craft detailed components like smart device housings, cam bodies, and power device coverings. Its accuracy is remarkable, with limited resistances as much as 0.01 mm, guaranteeing flawless item setting up. This alloy's exceptional corrosion resistance makes it an outstanding choice for exterior applications, making sure resilient, resilient items in the pointed out sectors.
Some Of Alcast Company
The aluminum alloy you choose will considerably impact both the casting process and the buildings of the last item. Due to the fact that of this, you should make your choice meticulously and take an educated strategy.
Establishing the most suitable light weight aluminum alloy for your application will certainly imply weighing a vast variety of characteristics. The first group addresses alloy features that impact the manufacturing procedure.
Alcast Company - Questions
The alloy you select for die casting directly impacts a number of aspects of the casting procedure, like exactly how easy the alloy is to collaborate with and if it is prone to casting defects. Hot cracking, also referred to as solidification cracking, is a typical die casting problem for aluminum alloys that can lead to internal or surface-level splits or splits.
Particular aluminum alloys are extra prone to warm breaking than others, and your choice should consider this. One more usual flaw found in the die spreading of light weight aluminum is pass away soldering, which is when the actors sticks to the die wall surfaces and makes ejection tough. It can damage both the actors and the die, so you should search for alloys with high anti-soldering residential or commercial properties.
Rust resistance, which is currently a notable quality of light weight aluminum, can vary considerably from alloy to alloy and is a necessary characteristic to think about depending upon the environmental conditions your item will certainly be subjected to (aluminum casting company). Wear resistance is one more residential property generally looked for read the full info here in light weight aluminum products and can set apart some alloys
Report this page